Our Services
Uptime LLC empowers your plant, new or existing, to achieve maximum uptime through a comprehensive suite of asset management tools. Our data-driven approach leverages four key areas to ensure your equipment operates at peak efficiency.
​
-
Reliability analysis to identify critical equipment vulnerabilities.
-
Custom maintenance plans tailored to each asset's needs.
-
GE APM integration for optimized preventive maintenance routines.
-
AVEVA software support to leverage advanced predictive maintenance.
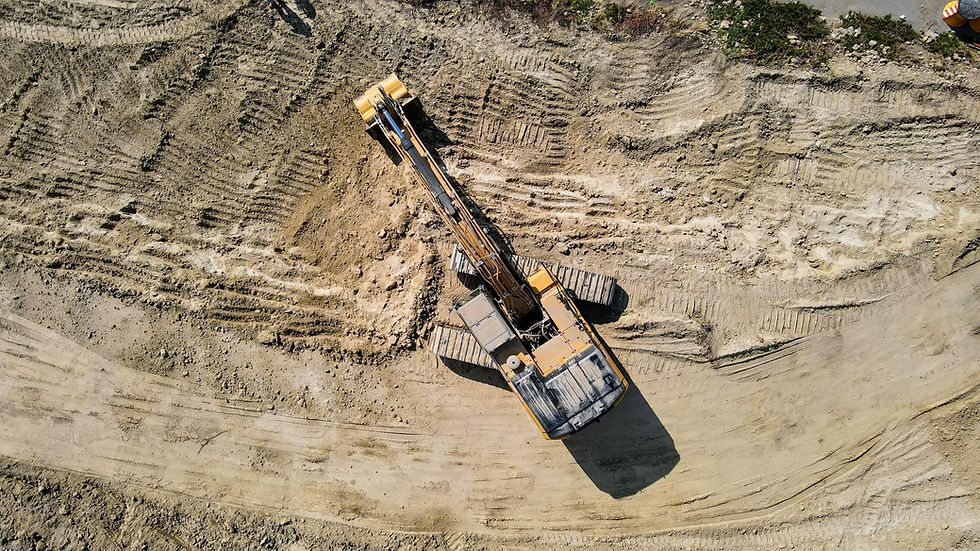
Reliability Centered Maintenance (RCM) Analysis
At Uptime, we understand the critical role of reliable assets in ensuring smooth operations and maximizing productivity. Our team of experienced engineers is dedicated to supporting MRO teams in building and improving Reliability-Centered Maintenance (RCM) programs for your plant's fixed and rotating equipment.
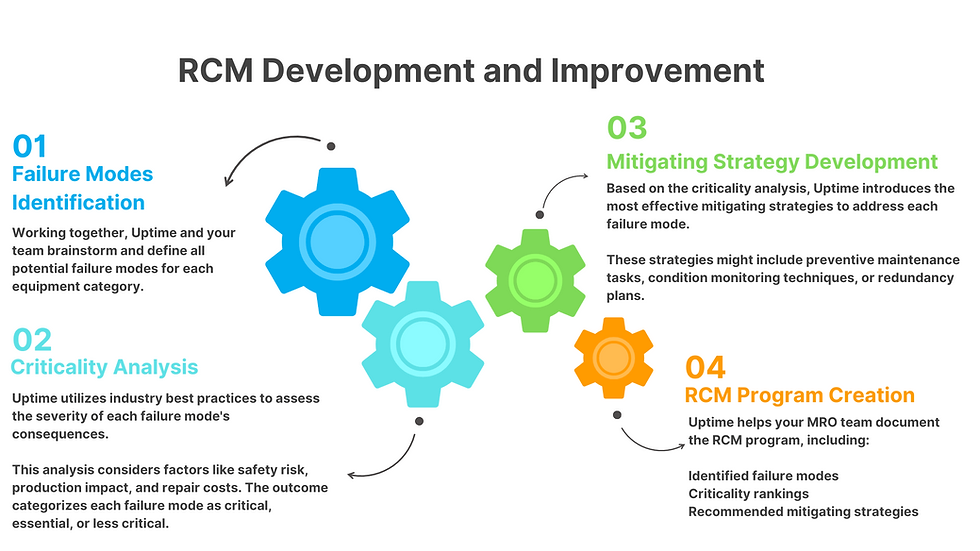.png)
Tailored Maintenance Tactics
At Uptime, we go beyond RCM program development. We leverage the RCM table to create a comprehensive and efficient maintenance plan for your plant's critical assets.
Our Approach outlines a six-step process for implementing a comprehensive critical equipment maintenance program. The steps are designed to ensure optimal uptime and performance of critical assets through a combination of proactive maintenance strategies and spare parts management.
Here’s a breakdown of the steps:
-
​
-
Step 6: Calculating Inventory Levels
.png)
Preventive Maintenance with GE APM
By leveraging the expertise of the UpTime team, GE's Asset Performance Management (APM) software automates tasks by utilizing the detailed maintenance procedures they gather and upload. This streamlines various maintenance and management processes, leading to significant improvements in efficiency and cost reduction.
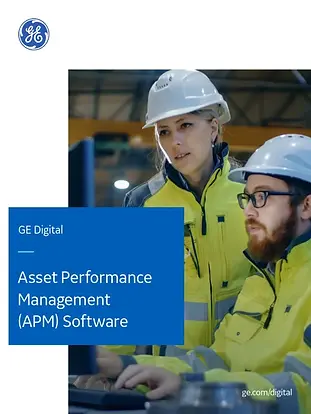

Reduced Manual Work:
Repetitive tasks like data entry, generating work orders, and scheduling preventive maintenance can be automated. This frees up valuable time for technicians to focus on actual repairs and troubleshooting, maximizing their expertise.
Improved Accuracy:
Manual data entry is prone to errors. Automation ensures data is collected and processed accurately, leading to more reliable insights and informed decision-making for maintenance activities.
Streamlined Workflows:
Automating tasks creates a smoother flow from identifying potential issues to scheduling maintenance and completing repairs. This reduces delays and ensures critical actions are taken promptly, minimizing downtime and potential equipment failures.
Automated Reporting:
Automated reports can be generated on asset health, maintenance history, and key performance indicators (KPIs). This allows for better visibility into asset performance and facilitates data-driven decision making for maintenance strategies and resource allocation.
By automating work processes, GE's APM software helps organizations achieve significant efficiency gains and cost reductions in asset management. This translates to improved asset reliability, reduced downtime, and optimized maintenance spending.

Predictive Maintenance with AVEVA Software
UpTime Services leverages AVEVA's cutting-edge predictive analytics software to revolutionize asset management. Our team of experts crafts sophisticated data-driven models that enable:
Proactive Maintenance
By analyzing real-time data, we identify anomalies and diagnose potential issues early, allowing for targeted maintenance before problems escalate.

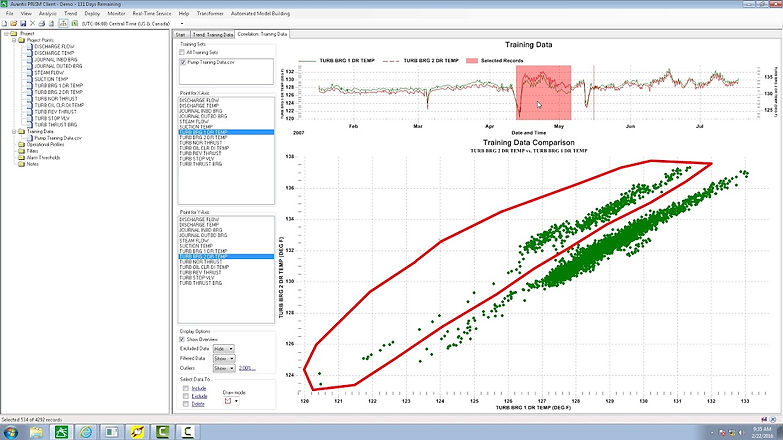.jpg)
Optimized Schedules
This proactive approach allows us to optimize preventive maintenance schedules, reducing unnecessary interventions and associated costs.
Maximized Uptime
Early detection and optimized maintenance lead to maximized asset uptime, ensuring your operations run smoothly and efficiently.
By partnering with UpTime Services, you gain a multitude of benefits
​
Early Fault Detection:
Identify and address potential issues before they snowball into major problems.
​
Improved Maintenance Planning:
Schedule maintenance strategically, minimizing disruptions and optimizing resource allocation.
​
Reduced Operational Risks & Costs:
Proactive maintenance lowers the risk of unexpected breakdowns and associated repair costs.
​
Increased Asset Availability & Productivity:
By maximizing uptime, your assets are available when needed, leading to increased productivity.
